Von dem „Torf“ im Achtersteven hatten wir ja schon an anderer Stelle berichtet. Inzwischen ist klar: Wir müssen ein Stück des Achterstevens austauschen, da wohl vor 60 Jahren (oder so) eine nicht ganz fachgerechte Reparatur durchgeführt wurde. Hierbei wurde Wasser oberhalb des Stevens eingeschlossen, so dass dieser Jahr für Jahr rotten konnte. So wird selbst die härteste Eiche weich.
Da im Laufe der Zeit, wie meist üblich, die Spantenenden zur Bilge hin abgerottet sind, müssen wir diese erst ersetzen, um die Form der Planken wieder hinzubekommen und Referenzpunkte für den Steven zu haben.
Bei dieser Reparatur streiten sich „die Gelehrten“, was die „richtige“ Variante ist: Vollholz im Dampf „einbiegen“ oder Formverleimen. Wir haben beides schon praktiziert, wobei ich das Dampfbiegen nur bei ganzen Spanten machen würde (der Originalität wegen). Bei den Köpfen, die oft auch wegen der engen Radien nach dem Biegen brechen, bevorzuge ich das Formverleimen. Zum einen brechen diese Spanten nicht wieder, zum anderen brauche ich beim „Dampfen“ frisches Holz, welches sich dann sehr lange nicht über eine Schäftung mit den Original-Spanten verleimen lässt, weil es zu nass ist. Das heißt, ich kann es nur paralell überlappend zu den Original-Spanten setzen, was ich nicht so schön finde. Aber hier kann jeder für sich entscheiden, was er für richtig hält.
Heute geht es also um das Herstellen formverleimter Spanten(köpfe):
Als erstes müssen wir von der Stelle, an der der Spant sitzen soll, eine Schablone abnehmen. Dies kann einfach in Pappe oder Hartfaserplatte geschehen. Erst grob anzeichnen und ausschneiden, dann die Schablone anlegen und den Stift auf die Planken legen und schön gleichmäßig die genaue Kontur anreißen. Nachschneiden, kontrolieren, ggf. nochmals nacharbeiten, fertig.
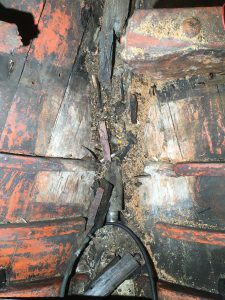
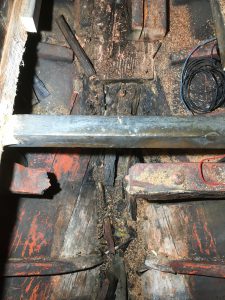
Von diesen Schablonen kann man dann eine Form abnehmen. Das kann je nach Form und Größe so wie bei uns ein Holzklotz sein, den man aussägt, oder aber auch Holzklötze, die man auf eine Platte schraubt und die die Form der Schablone (oder wenn es geht direkt des Objektes) aufnehmen. So haben wir zum Beispiel schon formverleimte Pinnen, Relinge etc. gefertigt (für andere Projekte).
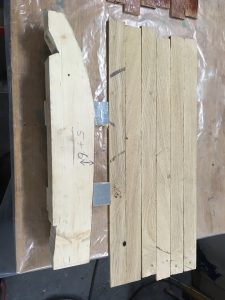
Achtung! Immer darauf achten, dass die Schraubzwingen, mit denen wir die Lamellen in Form bringen, eine Auflagefläche von ca. 90 Grad zu dem verleimten Teil haben. Deswegen die „Absätze“ auf der Unterseite der Form.
Nun müssen wir noch das Holz für die Lamellen herstellen. Wir nehmen hier wie Original Eiche, eines der durch die im Holz vorhandenen Gerbsäuren verottungsbeständigen heimischen Hölzer.
Nachteil dieser Gerbsäuren ist, dass es zu Problemen mit Epoxi als Leim kommen könnte. Wir wollen es genau wissen (für die Zukunft) und bauen einen Spant mit Epoxi, wobei wir das Holz vorher im Leimflächenbereich von den Säuren befreien, immer wieder mit Aceton abwaschen, bis der Lappen nicht mehr braun wird. Diesen Spant werden wir genauso weiterbehandeln wie die, die wir einbauen, um zu sehen, ob es in den nächsten Jahren Probleme hiermit geben wird.
Für die „richtigen“ Spanten verwenden wir ein sehr altes Produkt, Bindan-Cin, einen Resorcinharzleim, 2 Komponenten (rotbraunes Harz und weißes Pulver), welches schon in meiner Jugend (also vor 40 Jahren) zum Verleimen seewasserfester, hochbelastbarer Verleimungen genommen wurde und heute noch Anwendung findet. Inzwischen darf dieser aber aus Gesundheitsgründen bei der Verarbeitung nur noch von gewerblichen Anwendern genutzt und erworben werden.
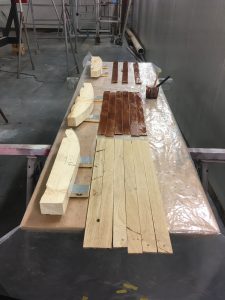
Hier habe ich die drei Formen auf dem Tisch, davor jeweils die Lamellen. Hier allerdings schon in verschiedenen Arbeitsschritten. Doch der Reihe nach.
Wir Rühren uns den Leim an. Dieser muss beidseitig aufgetragen werden und jeweils nach dem Auftrag 15 Minuten ablüften (wichtig!). Danach kann ich jeweils zwei Lamellen aufeinanderlegen, dann jeweils wieder die Oberseite beider Doppelstapel einstreichen. Diese drei Stadien sehe ich auf dem obigen Bild.
Vorne: Vorbereitet zum Streichen.
Mitte: Alle Hölzer einseitig eingestrichen (sie lüften ab).
Hinten: Die ersten Leisten sind aufeinandergestapelt, deren Oberseite dann wieder eingestrichen.
Nun wird nach dem Ablüften noch der mittlere Stapel auf den seitlichen gelegt, wieder oben eingepinselt und nach dem Ablüften kommt der letzte Stapel obenauf.
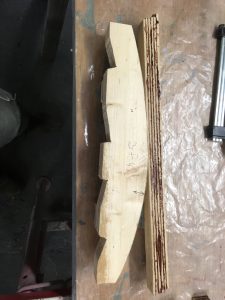
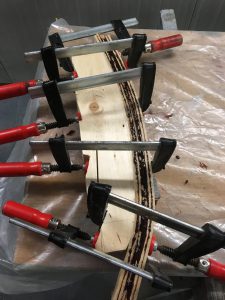
Gut erkennt man hier auch die Auflageflächen der Zwingen in den Biegungen. Wäre die Form hier einfach gerade, würden die Zwingen abrutschen!